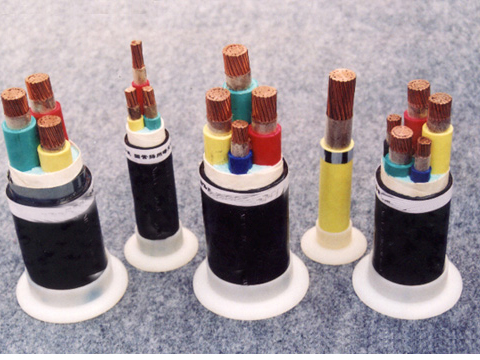
The performance of the flame-retardant cable is determined by the oxygen index of the material it uses. The higher the oxygen index, the better the flame-retardant performance of the flame-retardant cable. But at the same time, some of the other properties will be lost, increasing the difficulty of operation and material costs. The experimental requirements of Class C through the standard bell require that the oxygen index of the insulating material reach 30, and that the flame-retardant materials are used if both Class B and Class A jacket materials and filler materials are to be achieved.
Flame-retardant cables mainly use halogen-free flame retardant materials and halogen-containing flame retardant materials
1, halogen-free flame retardant materials
Polyolefins are halogen-free materials composed of hydrocarbons that decompose carbon dioxide and water during combustion without producing significant fumes and harmful gases. Polyolefins mainly include polyethylene (PE) and ethylene vinyl acetate olefin (E-VA). These materials are not inherently flame-retardant and require the addition of inorganic flame retardants and phosphorus flame retardants in order to be processed into practical halogen-free flame retardant materials. However, due to the lack of polar groups in the molecular chains of non-polar substances. It is hydrophobic and has poor affinity with inorganic flame retardants, making it difficult to bind firmly. In order to improve the surface activity of the polyolefin, a surfactant may be added to the formulation; or a polymer containing a polar group may be blended in the polyolefin for blending, thereby increasing the amount of the flame retardant filler and improving the mechanical properties of the material. Processing performance, while achieving better flame retardancy.
2, low smoke low halogen flame retardant material
Mainly for polyvinyl chloride and chlorosulfonated polyethylene two materials. CaCO3 and A(lOH)3 were added to the PVC formulation. Zinc borate and MoO3 can reduce the release of HCL and the amount of fuming of flame-retardant PVC, thereby increasing the flame retardancy of the material and reducing the emissions of halogens, acid mist, and smog, but may cause a slight decrease in the oxygen index. When the amount of additives is large, the mechanical and electrical properties of the material are also reduced.
3, halogen-containing flame retardant materials
Since the hydrogen halide is released when the combustion heats, the hydrogen halide can capture the active radical HO radical, thereby delaying or extinguishing the combustion of the material and achieving the purpose of flame-retardant. Commonly used polyvinyl chloride, chloroprene rubber, chlorosulfonated polyethylene, ethylene propylene rubber and other materials.
(1) Flame-retardant polyvinyl chloride (PVC): Because of its low price, good insulation performance and good flame retardancy, PVC is widely used in ordinary flame-retardant wire and cable. In order to improve the flame retardancy of PVC, a halogen flame retardant (decabromodiphenyl ether), chlorinated paraffin, and a synergistic flame retardant are often added to the formulation to improve the flame retardancy of polyvinyl chloride.
(2) Ethylene-propylene rubber (EPDM): Non-polar hydrocarbons, with excellent electrical properties, high insulation resistance, low dielectric loss, but ethylene propylene rubber is a flammable material, must reduce the degree of cross-linking of ethylene-propylene rubber, Reduce the low-molecular-weight substances generated by the breaking of the molecular chain to improve the flame retardant properties of the material. As the degree of cross-linking of ethylene-propylene rubber increases, the oxygen index increases. For example, in the formulation, a cross-linking agent DC (P-diisopropylbenzene peroxide), a cross-linking agent TAIC (tripropenyl cyanurate), and HVA (2N, N-m-phenylene bismaleimide) may be added to the formulation. Increase the oxygen index by 10-15. In another method, adding an inorganic flame-retardant filler to ethylene-propylene rubber can also increase the oxygen index. The commonly used fillers are A(lOH)3, which can release crystalline water at high temperatures, and absorb heat to achieve a flame retardant effect. However, the bulk addition of fillers can degrade the mechanical and electrical properties of the material (such as reduced tensile strength and elongation). Therefore, the filler cannot exceed 150 parts. In order to obtain better flame-retardant properties and maintain high mechanical properties, it is necessary to appropriately reduce the flame-retardant filler and appropriately increase other flame-retardants.
A Battery Management System (BMS) is any electronic system that manages a rechargeable battery (cell or battery pack), such as by protecting the battery from operating outside its Safe Operating Area, monitoring its state, calculating secondary data, reporting that data, controlling its environment, authenticating it and / or balancing it.
A battery pack built together with a battery management system with an external communication data bus is a smart battery pack. A smart battery pack must be charged by a Smart Battery Charger.
Battery Management System
Battery Management System,Bms Battery Management System,12V Battery Management System,Lipo Battery Management System
Xinxiang Taihang Jiaxin Electric Tech Co., Ltd , https://www.chargers.be