I. Introduction
As one of the main switching power devices, MOSFETs are widely used in module power supplies. Understanding the MOSFET loss composition and analyzing it helps to optimize the MOSFET loss and increase the power of the module power supply. However, blindly reducing the MOSFET loss and other losses will cause more serious EMI problems, and the entire system cannot work stably. . Therefore, the EMI performance of the module power supply needs to be taken into account while reducing the loss of the MOSFET.
Second, power analysis of switch tube MOSFET
MOSFET losses mainly consist of the following components: 1. On-state losses; 2. Conduction losses; 3. Turn-off losses; 4. Drive losses; 5. Absorption losses; Switching frequencies need to be reduced as the module power supply is reduced in size. Further improvement leads to increased turn-on loss and turn-off loss. For example, at 300 kHz drive frequency, the ratio of turn-on loss and turn-off loss is already a major part of the total loss.
Losses occur during turn-on and turn-off of the MOSFET. During these two conversions, the relationship between drain voltage and drain current, gate-to-source voltage, and charge are shown in Figures 1 and 2, which are now turned on. The conversion process is used as an example for analysis:
T0-t1 interval: The gate voltage rises from 0 to the threshold voltage Uth, the switch is turned on, and no drain current passes through this interval without loss;
T1-t2 interval: the gate voltage reaches Vth, the drain current ID begins to increase, reaches the maximum value at time t2, but the high level does not change when the drain-source voltage remains off. As can be seen from Figure 1, this part has VDS and ID overlap, MOSFET power consumption increases;
T2-t3 interval: From time t2, the drain-source voltage VDS begins to drop, causing a Miller capacitance effect, making the gate voltage unable to rise and appearing in the platform. The charge quantity at t2-t3 is equal to Qgd, and the drain voltage starts to decrease at time t3. Minimum; this part has VDS and ID overlap, MOSFET power consumption increases
T3-t4 interval: The gate voltage rises from the platform to the final drive voltage (the module power is generally set to 12V). The rising gate voltage further reduces the on-resistance, and the MOSFET enters the full-on state. At this time, the loss is converted into conduction. Pass loss.
The turn-off process is similar to the turn-on process, except that the waveforms are reversed. For the analysis of the turn-on and turn-off loss of the MOSFET, there are many references available. Here is a summary of the MOSFET analysis by Zhang Xingzhu as follows:
Remarks: The rise time, the switching frequency, the fall time, the gate charge, and the gate drive voltage are the MOSFET body diode losses.
Third, the MOSFET loss optimization method and its advantages and disadvantages
3-1. Reduce MOSFET Losses by Reducing the Drive Frequency of the Module Supply [Slightly Ask EMI Questions and Solutions]
It can be seen from the loss analysis of the MOSFET that the higher the driving frequency of the switching power supply, the higher the conduction loss, turn-off loss, and drive loss, but the higher frequency of the switching power supply can make the transformer core of the module power supply smaller and the module volume smaller. It becomes smaller, so the switching frequency can be optimized to optimize the turn-on loss, turn-off loss, and drive loss, but high frequency can cause serious EMI problems. Jinshengyang DC/DC R3 products adopt the frequency hopping control method to reduce the driving loss by reducing the switching frequency of the module power supply under light load conditions, thereby further improving the efficiency under light load conditions, making the system more energy-efficient under standby operation. To further improve the working time of the battery power supply system and also reduce the EMI radiation problem;
3-2. Reduce MOSFET loss by reducing
The circuit topology of a typical low-power module power supply (less than 50W) is in the flyback form, and the typical control circuit is shown in Figure 3. From the MOSFET loss analysis, it can also be known that it is proportional to the turn-on loss and turn-off loss. It is proportional to; so can reduce and reduce the loss of MOSFET, under normal circumstances, can reduce the driving resistance Rg of MOSFET to reduce, time, but this optimization method has brought serious EMI problem; Take Jin Shengyang URB2405YMD-6WR3 product as Example to illustrate this problem:
1) URB2405YMD-6WR3 uses 10Ω MOSFET driver resistance, bare-metal radiation test results are as follows:
2) URB2405YMD-6WR3 uses a 0Ω driving resistor. The bare-metal radiation test results are as follows:
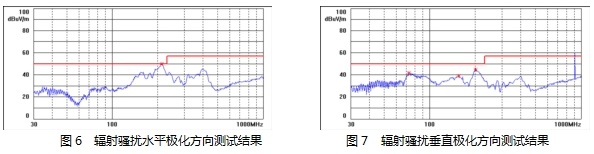
From the results of two different driving resistance tests, although all of them can pass the CLASS A level of radiation disturbance degree of EN55022, with a 0 ohm driving resistance, the test result margin in the horizontal polarization direction is less than 3dB. Plan design cannot be passed.
3-3. Reducing Loss by Reducing Absorption Circuit Losses
In the design process of the module power supply, the leakage inductance of the transformer is always present. Using a flyback topology, often there is a large voltage spike at the drain of the MOSFET during the MOSFET turn-off. Under normal circumstances, the MOSFET The voltage design margin is sufficient, and in order to improve the overall power efficiency, some power supply manufacturers do not increase the absorption circuit (absorption circuit as shown in Figure 3 with 1RCD absorption circuit and 2RC absorption circuit) to absorb the spike voltage. However, not paying attention to the design of these absorption circuits is often the main reason for the EMI design failure. Take Jin Shengyang's URF2405P-6WR3 absorption circuit (using the 2RC absorption circuit in Figure 3) as an example:
1) The drive resistance Rg is 27Ω, no RC absorption circuit, radiation disturbance test results are as follows:
2) The drive resistance is 27Ω; the absorption circuit is the resistance R and C 5.1Ω 470pF, and the radiation disturbance test results are as follows:
From the test results of two different absorption circuit schemes, the scheme that does not use an absorption circuit cannot pass the CLASS A level of EN55022 radiation harassment, and the use of an absorption circuit can solve the problem that the radiation irritability experiment does not pass. Different RC combinations can further reduce radiation disturbances.
Fourth, summary
The power optimization of MOSFETs is actually a system engineering, and some optimization schemes may even affect the characteristics of EMI. In the above case, Jin Shengyang's R3 series products penetrated the concept of energy conservation and environmental protection into the development process of the power supply, and well balanced the overall power supply efficiency and EMI characteristics, thereby further optimizing the power supply parameters. The power parameters are further optimized to be more compatible with the customer's system, and to play the "heart" role of the true electronic system, which continuously delivers energy.
, https://www.mosvapor.com